Dlaczego dystansowanie wyposażenia ochronnego jest tak istotne dla bezpieczeństwa operatora? Czym jest dobiegometr? Na te pytania odpowiada Tomasz Drewniok, CSM & Safety Business Consultant w RAContols.
W artykule poruszone zostaną najważniejsze kwestie dotyczące zastosowania wyposażenia ochronnego wraz ze wskazaniem obowiązujących norm oraz wzorów pozwalających wyliczyć odpowiednią odległość pomiędzy wybranym zabezpieczeniem a maszyną.
Obowiązek zapewnienia bezpieczeństwa operatora
Zagadnieniem często traktowanym powierzchownie w procesie oceny zgodności maszyny z dyrektywami dotyczącymi bezpieczeństwa (tzw. maszynowa i narzędziowa) jest prawidłowe dystansowanie wyposażenia ochronnego. Składa się na nie zarówno zachowanie prawidłowego bezpiecznego dystansu pomiędzy zagrożeniem, a wyposażeniem ochronnym, jak i wielkość oraz miejsce montażu, tak by obejście urządzenia ochronnego nie było możliwe.
Obowiązek ten dotyczy zarówno maszyn “nowych”, jak i “starych”. Wynika wprost z obowiązku zapewnienia bezpieczeństwa operatora pracującego na maszynie, dlatego status maszyny w rozumieniu dyrektyw w zasadzie nie ma wpływu na ocenę prawidłowego stosowania wyposażenia ochronnego. Jeśli została podjęta decyzja o tego rodzaju zabezpieczeniu strefy zagrożenia, należy wykonać je zgodnie z odpowiednia normą.
Wyposażenie ochronne: rodzaje, zasada działania, podstawa prawna
Do wyposażenia ochronnego zaliczamy między innymi: kurtyny i bariery świetlne, skanery laserowe, urządzenia sterowania oburęcznego, osłony blokujące, maty bezpieczeństwa, itp.
Aktywacja wyposażenia ochronnego następuje w zależności od rodzaju:
- w momencie otwarcia osłony blokującej
- gdy operator przetnie promień świetlny (w przypadku kurtyn i barier)
- wraz ze zwolnieniem dowolnego przycisku sterującego (w urządzeniach sterowania oburęcznego)
- w chwili, w której operator nastąpi na powierzchnię maty
Procedura dystansowania wyposażenie ochronnego wynika z normy PN-EN 13855 – Bezpieczeństwo maszyn – Umiejscowienie wyposażenia ochronnego ze względu na prędkości zbliżania części ciała człowieka.
Norma ta zawiera zalecenia co do montażu urządzeń oraz przede wszystkim wzory pozwalające na wyliczenie prawidłowej odległości bezpiecznej. Kalkulacja dystansowania wyposażenia ochronnego oparta jest o przyjęte prędkości ruchu kończyn oraz o czas zatrzymania elementów będących źródłem zagrożenia. Czas ten często określany jest jako czas wybiegu lub czas reakcji systemu bezpieczeństwa.
Elementami stwarzającymi zagrożenie mogą być siłowniki, rolki napędowe, urządzenia będące pod napięciem, itp.
Przykładowy łańcuch urządzeń związanych z zagrożeniem oraz wyposażeniem ochronnym poniżej:
Kurtyna świetlna
Przekaźnik bezpieczeństwa
Elektrozawór
Siłownik pneumatyczny
Jak wiadomo, zarówno dla kurtyn świetlnych, jak i przekaźników bezpieczeństwa producenci podają czas reakcji, który to parametr jest jak najbardziej wiarygodny i może zostać użyty do kalkulacji na etapie projektowania.
Takie wartości są podawane dla kurtyn i barier świetlnych, skanerów laserowych. Podobnie dla elementów logiki układu sterowania związanego z bezpieczeństwem łatwo można znaleźć odpowiednie dane. Dotyczy to np. przekaźników bezpieczeństwa, sterowników z wbudowaną funkcją bezpieczeństwa (CPU, karty wejścia i wyjściowe).
Należy pamiętać, że łączenie szeregowe elektronicznych urządzeń wejściowych również może powodować zwiększenie czasu wygenerowania sygnału zatrzymania (stan OFF) dla układu logiki.
Całkowity czas zatrzymania
Całkowity czas zatrzymania zgodnie z normą to:
T = t1 + t2
gdzie:
t1 – maksymalny czas pomiędzy otwarciem osłony (przecięciem promieni kurtyny świetlnej), a przejściem wyjść wyłącznika blokującego w stan OFF (wygenerowanie sygnału zatrzymania)
t2 – maksymalny czas od momentu wygenerowania sygnału zatrzymania przez układ wyposażenia ochronnego do momentu zatrzymania niebezpiecznego ruchu. W tym czasie mieści się również czas odpowiedzi (response time) układu sterowania maszyny.
Pomiar realnego czasu zatrzymania, rola dobiegometru
Pewnym utrudnieniem w projektowaniu dystansowania wyposażenia ochronnego są elementy, dla których w zasadzie niemożliwe jest podanie takiego parametru (całkowitego czasu zatrzymania), w związku z czym jedynym rozwiązaniem jest praktyczny pomiar na istniejącym układzie. Należą do nich mechaniczne elementy wykonawcze (elementy napędzane poprzez siłowniki, silniki, itp).
Rzeczywisty czas zatrzymania elementów wykonawczych zależy do wielu czynników, takich jak: masa (często zmienna), prędkość, ciśnienie medium zasilającego, czas przełączania styczników lub elektrozaworów, dlatego zachodzi konieczność pomiaru w warunkach rzeczywistej pracy. Co więcej, doświadczenia z pomiarów mogą stanowić bazę dla procesów projektowania urządzeń o zbliżonej konstrukcji. Ostateczna walidacja dla poszczególnych maszyn jest jednak zalecana, a w wielu przypadkach wręcz wymagana przez użytkowników.
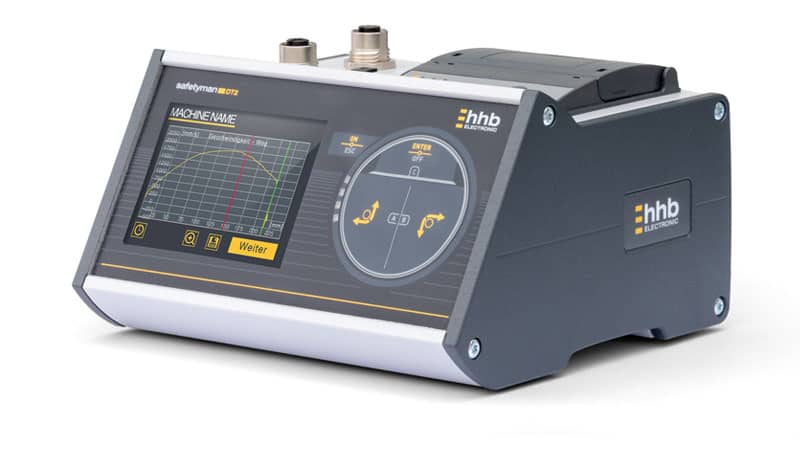
Urządzeniem dedykowanym do mierzenia realnego czasu zatrzymania tego typu układu jest dobiegometr (na zdjęciu powyżej). Urządzenie mierzy na bieżąco ruch elementu stwarzającego zagrożenie np. za pomocą enkodera linkowego przymocowanego do suwaka prasy pneumatycznej.
Drugą ważną funkcją dobiegometru jest symulacja zatrzymania ruchu wraz z pomiarem jego czasu. Do symulacji może służyć aktywator w postaci mechanizmu z przesłoną (flagą) montowany na kurtynie świetlnej.
Moment wyzwolenia aktywatora (przecięcie promieni kurtyny) wyznacza się na podstawie analizy ruchu elementu. Zasadniczo moment ten wyznacza się po osiągnięciu maksymalnej prędkości elementu (np. suwaka prasy).
Dystansowanie wyposażenia ochronnego
Należy pamiętać, że dystansowanie wyposażenia ochronnego ściśle wiąże się z zagadnieniem możliwości sięgania poprzez wyposażenie (próby obejścia).
W tym przypadku kryteria instalacji wyposażenia określa norma PN-EN ISO 13857 – Bezpieczeństwo maszyn – Odległości bezpieczeństwa uniemożliwiające sięganie kończynami górnymi i dolnymi do stref niebezpiecznych.
Ciekawym przypadkiem jest prawidłowa instalacja wyłączników blokujących (wyłączniki krańcowe, magnetyczne, RFiD) na osłonach blokujących.
W przypadku zastosowania np. wyłącznika magnetycznego na osłonie należy pamiętać o momencie wygenerowania sygnału zatrzymania do maszyny. Ze względu na histerezę samego czujnika przejście czujnika w stan OFF następuje po oddaleniu aktywatora na odległość ok. 20 mm.
W tym czasie pomiędzy osłoną a konstrukcją może powstać szczelina. Norma PN-EN ISO 13857 stanowi, że w przypadku powstania szczeliny większej niż 20 mm konieczne jest dodanie dodatkowego dystansu 850 mm, co może stanowić problem dla maszyn usytuowanych na małej przestrzeni.
Prawidłowe ustawienie aktywatora względem wyłącznika pozwala na eliminację tego wymogu.
Wytyczne dotyczące omijania optoelektronicznych urządzeń (kurtyny, bariery, skanery) są bezpośrednio określone w normie PN-EN ISO 13855.
Przykładowa kalkulacja
Poniżej przedstawiona została przykładowa kalkulacja odległości bezpiecznej dla układu wyposażonego w kurtynę świetlną pionową o rozdzielczości 30mm. Zmierzony czas zatrzymania układu to 103 ms.
Wzór do określenia bezpiecznego dystansu to:
S = ( K x T) + C
gdzie:
S – dystans bezpieczeństwa [mm]
K – stała wynosząca 2000 mm/s (na podstawie prędkości ruchu ręki)
T – całkowity czas zatrzymania [sek]
C – dodatkowy dystans wynikający ze wzoru C= 8 ( d -14 ), nie może być mniejszy niż 0
d – rozdzielczość kurtyny [mm]
Wyliczenie bezpiecznego dystansu na podstawie przedstawionych powyżej parametrów:
S = (2000 x 0,103 ) + 8 ( 30 – 14 ) = (2000 x 0,103) + 128 = 332 mm
Oznacza to, że minimalna odległość pomiędzy najbliższym zagrożeniem a linią promieni kurtyny musi wynieść 332 mm.
Jeśli warunek ten nie będzie spełniony konieczne jest podjęcie działań technicznych zmniejszających czas zatrzymania układu lub oddalenie samej kurtyny, co zazwyczaj wiąże się ze zmianą całej konstrukcji obudowy maszyny.
Należy pamiętać, że w zależności od typu urządzenia i sposobu montażu stosuje się różne wzory i parametry do obliczeń. Poniżej przykłady wzorów stosowanych dla typowego wyposażenia ochronnego. Szczegółowe informacje znajdują się w normie PN-EN ISO 13855.
Wzory dla różnego typu urządzeń zabezpieczających
Zachęcamy do zapoznania się ze wzorami odpowiednimi dla różnego typu urządzeń zabezpieczających.
S = K x ( t1 + t2 ) + C
gdzie:
Parametr K = 1600 mm/s
Parametr C wynosi:
- w przypadku urządzeń sterowania oburęcznego – 250 mm dla przycisków bez dodatkowej osłony
- w przypadku osłony blokującej jest to dodatkowa odległość wynikająca z normy PN-EN ISO 13857
S = K x ( t1 + t2) + 8 x ( D – 14 mm )
gdzie:
Parametr K = 2000 mm/s
Parametr D to rozdzielczość kurtyny.
np. dla kurtyny 30 mm dodatkowy dystans wyniesie 128 mm.
S = K x (t1 + t2) + ( 1200 mm – 0,4 x H )
gdzie:
Parametr K = 1600 mm/s
Parametr H to odległość od podłoża.
Dodatkowy dystans nie może być mniejszy od 850 mm.
S = K x ( t1 + t2 ) + 850 mm
gdzie:
Parametr K = 1600 mm/s
Osłona blokująca, urządzenie blokujące
Warto w tymi miejscu przypomnieć, czym jest osłona blokująca oraz urządzenie blokujące.
Osłona blokująca
Osłona sprzężona z urządzeniem blokującym (np. wyłącznikiem bezpieczeństwa) w taki sposób, że:
- stwarzające zagrożenie funkcje maszyny nadzorowane przez tę osłonę nie mogą być realizowane do chwili zamknięcia osłony,
- otwarcie osłony w czasie, gdy maszyna realizuje funkcje stwarzające zagrożenie, powoduje wyzwolenie sygnału ich zatrzymania,
- stwarzające zagrożenie funkcje maszyny nadzorowane przez osłonę mogą być realizowane w czasie, gdy jest ona zamknięta, jednakże samo zamknięcie osłony nie powoduje rozpoczęcia ich realizacji.
Urządzenie blokujące (wyłącznik bezpieczeństwa)
wyłącznik krańcowy w wykonaniu specjalnym służący do monitorowania stanu urządzenia (np. osłony).
Wyłącznik taki musi spełniać warunek wymuszonego rozwarcia styku (osiągnięcie rozwarcia jako bezpośredniego skutku przez elementy niesprężyste).
Podsumowanie
Przede wszystkim należy pamiętać, że prawidłowe umiejscowienie i dystansowanie wyposażenia ochronnego jest szczegółowo opisane w normie PN-EN ISO 13855, w związku z czym otrzymujemy jasne wytyczne do oceny zgodności.
Zastosowane stałe do wzorów wynikają z badań statystycznych oraz wiedzy inżynierskiej ugruntowanej przez lata. Wbrew pozorom nie zawsze są to wytyczne bardzo rygorystyczne. Dla przykładu: rzeczywista, możliwa do osiągnięcia prędkość zbliżania się ręki do kurtyny świetlnej może przekroczyć 2000 mm/s, a jednak taką prędkość stosujemy we wzorze.
Stosowanie się do zaleceń normy gwarantuje poprawność wykonania. Jeżeli nie masz pewności, czy twoje przedsiębiorstwo spełnia założenia wynikające z dyrektyw dotyczących bezpieczeństwa, zapraszamy do skorzystania ze świadczonej przez RAControls usługi audytu. Pamiętajmy, że bezpieczeństwo obsługi maszyn jest jednym z priorytetów działań nowoczesnego zakładu produkcyjnego.
Firma RAControls bezpłatną prezentację dobiegometru wraz z omówieniem zasad pomiaru dobiegu w Państwa zakładzie. Szczegółowych informacji udzielą doradcy techniczni i handlowi RAControls.